OSHA Issues Two Standards to Protect Workers from Exposure to Respirable Crystalline Silica
November 2, 2017 | Brandon Neilson, CIH
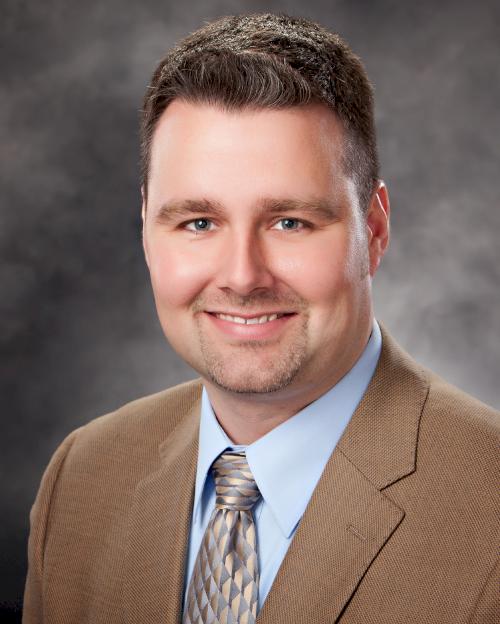
OSHA has issued a new crystalline silica rule as two standards—one for the construction industry and one for general industry and maritime. The OSHA Crystalline Silica Standard for the construction industry went into effect on September 23, 2017. This immediately affects the construction industry and will affect the general industry on June 23, 2018.
Some interesting facts regarding crystalline silica:
- It can be found in brick and mortar, any type of concrete, slate, granite, engineered stone, gravel aggregate, roofing granules, plastic composites and other building materials like drywall, plaster or even caulk.
- The size of the particles of concern is 100x smaller than a grain of sand.
- Recently surveyed ready-mix concrete plants indicated 74% are currently above the new Permissible Exposure Limit. (OSHA)
- Crystalline silica is a known hazard for silicosis, which is an incurable lung disease caused by breathing in silica.
The new construction industry standard already in effect requires all employers to have a written exposure control plan, and each company is to have a competent person on staff trained in crystalline silica. The general industry standard taking effect in June 2018 will require a written exposure control plan.
Several key points of the written exposure include identifying all tasks that present a potential exposure risk and control methods to protect workers. Exposure monitoring, medical surveillance and training are also requirements of the new standard.
In lieu of exposure monitoring, an employer may opt to follow the control methods listed within Table 1 of the construction standard. OSHA developed Table 1, which identifies: equipment/tasks, suitable engineering and work practice control methods and associated required respiratory protections. If an employer strictly adheres to the Table 1 guidelines, then exposure monitoring is not necessary. However, the additional medical surveillance and training are still required.
As mentioned above, a competent person will be required within a company to implement the written exposure control plan. The competent person will need to be knowledgeable on crystalline silica, the associated standards, potential exposure risks and various mitigation and/or control measures.
Additional Resources:
OSHA Fact Sheet – OSHA’s Crystalline Silica Rule: Construction
OSHA Fact Sheet – OSHA’s Crystalline Silica Rule: General Industry
Regulatory Standards:
29 CFR 1910.1053 – General Industry
29 CFR 1926.1153 – Construction Industry
Brandon Neilson, CIH, is a principal at Impact7G in Clive, Iowa. Contact him via email at bneilson@impact7g.com.