Labor Shortages Climb and Manufacturers Get Innovative
September 14, 2017 | Tom Brown
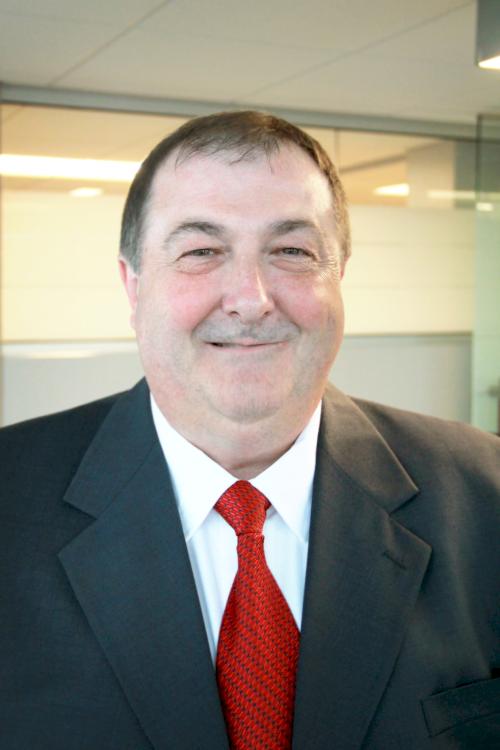
How Manufacturers Across the Industrial Sector are Surviving—and Thriving—Amidst a Weak Labor Market
Baby-boomer retirement, absenteeism, failed drug-screening, and both the lack of and “brain drain” of technically skilled workers out of the manufacturing sector have been implicated as contributing factors driving the nation’s unhealthy labor market. True to the solutions-driven nature of industry, business leaders, facility managers, and A/E professionals are joining forces to identify strategies to overcome this seemingly crippling labor shortage. Here, we explore a few.
Process and Equipment Layout Improvements
To limit or reduce labor needs, look no further than the production floor. Operations across production, product movement, storage, and distribution can all be improved by adjusting layouts and processes to better support the individual tasks being performed—often times within existing facility footprints.
For example, transitioning assembly lines from a traditional linear track to a U- or S-shape configuration may make it quicker, and more ergonomically sound, for product movers, who are then able to travel shorter distances across each line end. Over in warehousing, strategically reworking rack storage can significantly increase efficiencies while potentially recovering valuable square footage thanks to optimized layout design. Both reduce the need for additional labor, and add value to the overall process workflow.
Automation Technology
Beyond removing humans from some of the most dangerous, ergonomically stressful activities, automation has monumental impacts on overall efficiencies and optimization, while also introducing attractive opportunities for diversified, technically skilled positions with higher pay-grades.
It’s important to note that accommodating large—and potentially harmful—automation machinery demands a specific amount of production floor space, as well as higher paid technical workers to operate and maintain equipment. That’s why it’s important businesses looking to reduce manual labor on-site weigh the benefits of automation with potential impacts to facility footprint, production disruptions, and wages to accommodate higher-skilled employees. This brings us to strategy #3: Long-term facility planning.
Long-term Facility Planning
All too often, facility managers looking to expand operations struggle to maneuver around a line or employee entrance that was constructed without considering the long-term cost and programming implications of these short-sighted designs. As a result, many are forced to implement facility designs that reduce efficiencies and increase footprints.
Working with an experienced A/E firm to develop master plans and facility assessments can help avoid such obstacles by identifying each plant’s growth goals for the next five, 10, and 20 years, and ensuring more immediate building improvements accommodate future expansions.
Industry, by definition, is taking action. What strategic moves can we make to keep American manufacturing alive and well in today’s labor market?
Tom Brown is an Industrial and Food Processing Advisor at ISG. For more information please visit www.is-grp.com or contact Tom via email at tom.brown@is-grp.com.